Hybrid Electrical Vehicles
Introduction
- A hybrid electric vehicle (HEV) has two types of energy storage units, electricity and fuel.
- Electricity means that a battery (sometimes assisted by ultracaps) is used to store the energy, and that an electromotor (from now on called motor) will be used as traction motor.
- Fuel means that a tank is required, and that an Internal Combustion Engine (ICE, from now on called engine) is used to generate mechanical power, or that a fuel cell will be used to convert fuel to electrical energy.
- In the latter case, traction will be performed by the electromotor only.
- In the first case, the vehicle will have both an engine and a motor.
HEV classification
- Depending on the drive train structure (how motor and engine are connected), we can distinguish between
- parallel,
- series
- combined HEVs.
- Depending on the share of the electromotor to the traction power, we can distinguish between
- mild or micro hybrid (start-stop systems),
- power assist hybrid,
- full hybrid and plug-in hybrid.
- Depending on the nature of the non-electric energy source, we can distinguish between combustion (ICE),
- fuel cell, hydraulic or pneumatic power, and human power.
- spark ignition engines (gasoline) or compression ignition direct injection (diesel) engine.
- In the first two cases, the energy conversion unit may be powered by gasoline, methanol, compressed natural gas, hydrogen, or other alternative fuels.
Motors are the “work horses” of Hybrid Electric Vehicle drive systems. The electric traction motor drives the wheels of the vehicle.
- Unlike a traditional vehicle, where the engine must “ramp up” before full torque can be provided, an electric motor provides full torque at low speeds.
- The motor also has low noise and high efficiency. Other characteristics include excellent “off the line” acceleration, good drive control, good fault tolerance and flexibility in relation to voltage fluctuations.
- The front-running motor technologies for HEV applications include –
- PMSM (permanent magnet synchronous motor),
- BLDC (brushless DC motor),
- SRM (switched reluctance motor) and
- AC induction motor.
- A main advantage of an electromotor is the possibility to function as generator. In all HEV systems, mechanical braking energy is regenerated.
- The max. operational braking torque is less than the maximum traction torque; there is always a mechanical braking system integrated in a car.
The battery pack in a HEV has a much higher voltage than the SIL automotive 12 Volts battery, in order to reduce the currents and the I2R losses.
Accessories such as power steering and air conditioning are powered by electric motors instead of being attached to the combustion engine. This allows efficiency gains as the accessories can run at a constant speed or can be switched off, regardless of how fast the combustion engine is running.
Especially in long haul trucks, electrical power steering saves a lot of energy.
1. Types by drivetrain structure
a) Series hybrid
In a series hybrid system, the combustion engine drives an electric generator (usually a three-phase alternator plus rectifier) instead of directly driving the wheels. The electric motor is the only means of providing power to the wheels. The generator both charges a battery and powers an electric motor that
moves the vehicle. When large amounts of power are required, the motor draws electricity from both the batteries and the generator.

Series hybrid configurations already exist a long time: diesel-electric locomotives, hydraulic earth moving machines, diesel-electric power groups, loaders.
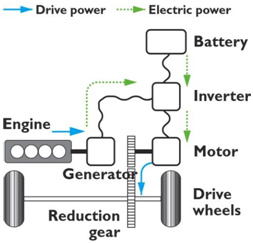
Structure of a series hybrid vehicle(below with flywheel or ultracaps as peak power unit)

Series hybrids can be assisted by ultracaps (or a flywheel: KERS=Kinetic Energy Recuperation System), which can improve the efficiency by minimizing the losses in the battery. They deliver peak energy during acceleration and take regenerative energy during braking. Therefore, the ulracaps are kept charged at low speed and almost empty at top speed. Deep cycling of the battery is reduced, the stress factor of the battery is lowered.
A complex transmission between motor and wheel is not needed, as electric motors are efficient over a
wide speed range. If the motors are attached to the vehicle body, flexible couplings are required.
Some vehicle designs have separate electric motors for each wheel. Motor integration into the wheels has the disadvantage that the unsprung mass increases, decreasing ride performance. Advantages of individual wheel motors include simplified traction control (no conventional mechanical transmission elements such as gearbox, transmission shafts, differential), all wheel drive, and allowing lower floors, which is useful for buses. Some 8×8 all-wheel drive military vehicles use individual wheel motors.
A fuel cell hybrid electric always has a series configuration: the engine-generator combination is replaced by a fuel cell.

Structures of a fuel cell hybrid electric vehicle
Weaknesses of series hybrid vehicles:
The ICE, the generator and the electric motor are dimensioned to handle the full power of the vehicle. Therefore, the total weight, cost and size of the powertrain can be excessive.
The power from the combustion engine has to run through both the generator and electric motor. During long-distance highway driving, the total efficiency is inferior to a conventional transmission, due to the several energy conversions.
Advantages of series hybrid vehicles:
There is no mechanical link between the combustion engine and the wheels. The engine- generator group can be located everywhere.
There are no conventional mechanical transmission elements (gearbox, transmission shafts).
Separate electric wheel motors can be implemented easily.
The combustion engine can operate in a narrow rpm range (its most efficient range), even as the car changes speed.
Series hybrids are relatively the most efficient during stop-and-go city driving.
Example of SHEV: Renault Kangoo.
b)Parallel hybrid
Parallel hybrid systems have both an internal combustion engine (ICE) and an electric motor in parallel connected to a mechanical transmission.

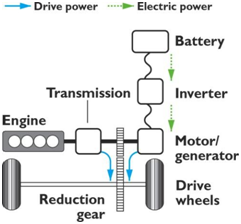
Structure of a parallel hybrid electric vehicle

Most designs combine a large electrical generator and a motor into one unit, often located between the combustion engine and the transmission, replacing both the conventional starter motor and the alternator (see figures above). The battery can be recharged during regenerative breaking, and during cruising (when the ICE power is higher than the required power for propulsion). As there is a fixed mechanical link between the wheels and the motor (no clutch), the battery cannot be charged when the car isn’t moving.
When the vehicle is using electrical traction power only, or during brake while regenerating energy,
the ICE is not running (it is disconnected by a clutch) or is not powered (it rotates in an idling manner).

Operation modes:
The parallel configuration supports diverse operating modes:
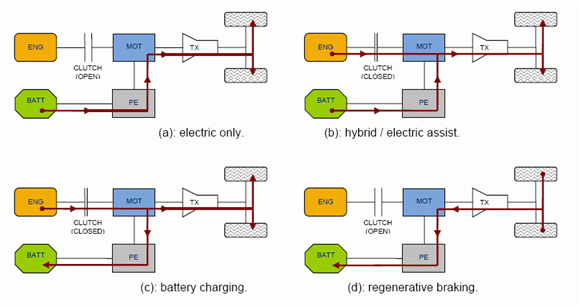
Some typical modes for a parallel hybrid configuration PE = Power electronics
TX = Transmission
- electric power only: Up to speeds of usually 40 km/h, the electric motor works with only the energy of the batteries, which are not recharged by the ICE. This is the usual way of operating around the city, as well as in reverse gear, since during reverse gear the speed is limited.
- ICE power only: At speeds superior to 40 km/h, only the heat engine operates. This is the normal operating way at the road.
- ICE + electric power: if more energy is needed (during acceleration or at high speed), the electric motor starts working in parallel to the heat engine, achieving greater power
- ICE + battery charging: if less power is required, excess of energy is used to charge the batteries. Operating the engine at higher torque than necessary, it runs at a higher efficiency.
- regenerative breaking: While braking or decelerating, the electric motor takes profit of the kinetic energy of the he moving vehicle to act as a generator.
Sometimes, an extra generator is used: then the batteries can be recharged when the vehicle is not driving, the ICE operates disconnected from the transmission. But this system gives an increased weight and price to the HEV.
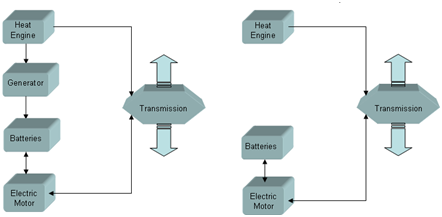
A parallel HEV can have an extra generator for the battery (left) Without generator, the motor will charge the battery (right)
Weaknesses of parallel hybrid vehicles: Rather complicated system.
The ICE doesn’t operate in a narrow or constant RPM range, thus efficiency drops at low rotation speed.
As the ICE is not decoupled from the wheels, the battery cannot be charged at standstill.
Advantages of parallel hybrid vehicles:
Total efficiency is higher during cruising and long-distance highway driving.
Large flexibility to switch between electric and ICE power
Compared to series hybrids, the electromotor can be designed less powerful than the ICE, as it is assisting traction. Only one electrical motor/generator is required.
Example of PHEV:
Honda Civic. Honda’s IMA (Integrated Motor Assist) uses a rather traditional ICE with continuously variable transmission, where the flywheel is replaced with an electric motor.
Influence of scale: a Volvo 26 ton truck (12 ton own weight, 14 ton max load) equipped with 200 kg of batteries can drive on pure electric power for 2 minutes only! Because of space constraints, it is not possible to build in more batteries.
BMW 7Series ActiveHybrid.
c)Combined hybrid
Combined hybrid systems have features of both series and parallel hybrids. There is a double connection between the engine and the drive axle: mechanical and electrical. This split power path allows interconnecting mechanical and electrical power, at some cost in complexity.
Power-split devices are incorporated in the powertrain. The power to the wheels can be either mechanical or electrical or both. This is also the case in parallel hybrids. But the main principle behind the combined system is the decoupling of the power supplied by the engine from the power demanded by the driver.
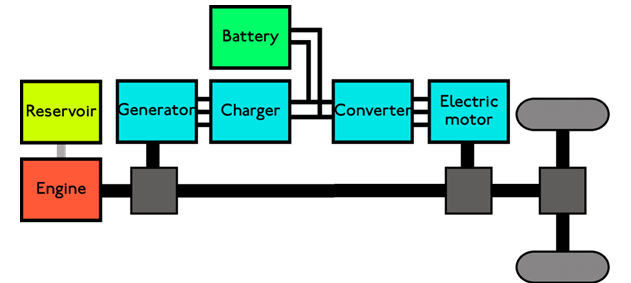
Simplified structure of a combined hybrid electric vehicle
In a conventional vehicle, a larger engine is used to provide acceleration from standstill than one needed for steady speed cruising. This is because a combustion engine’s torque is minimal at lower RPMs, as the engine is its own air pump. On the other hand, an electric motor exhibits maximum torque at stall and is well suited to complement the engine’s torque deficiency at low RPMs. In a combined hybrid, a smaller, less flexible, and highly efficient engine can be used. It is often a variation of the conventional Otto cycle, such as the Miller or Atkinson cycle. This contributes significantly to the higher overall efficiency of the vehicle, with regenerative braking playing a much smaller role.
At lower speeds, this system operates as a series HEV, while at high speeds, where the series powertrain is less efficient, the engine takes over. This system is more expensive than a pure parallel system as it needs an extra generator, a mechanical split power system and more computing power to control the dual system.

Combined HEV with planetary unit as used in the Toyota Prius
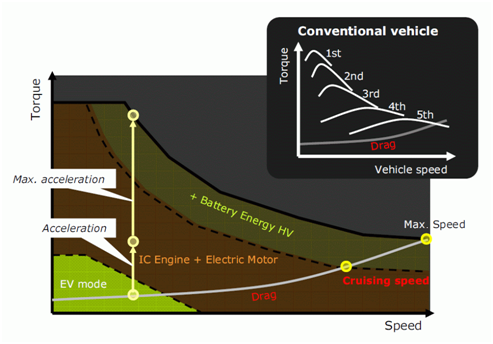
Combined hybrid drive modes
Weaknesses of combined hybrid vehicles:
Very complicated system, more expensive than parallel hybrid.
The efficiency of the power train transmission is dependent on the amount of power being transmitted over the electrical path, as multiple conversions, each with their own efficiency, lead to a lower efficiency of that path (~70%) compared with the purely mechanical path (98%).
Advantages of combined hybrid vehicles:
Maximum flexibility to switch between electric and ICE power
Decoupling of the power supplied by the engine from the power demanded by the driver allows for a smaller, lighter, and more efficient ICE design.
Example of CHEV: Toyota Prius, Auris, Lexus CT200h, Lexus RX400h.
2. Types by degree of hybridization
Parallel and combined hybrids can be categorized depending upon how balanced the different portions are at providing motive power. In some cases, the combustion engine is the dominant portion; the electric motor turns on only when a boost is needed. Others can run with just the electric system operating.

Overview of Hybrid-powertrain concepts
Strong hybrid ( = full hybrid)
A full hybrid EV can run on just the engine, just the batteries, or a combination of both. A large, high- capacity battery pack is needed for battery-only operation.
Examples:
The Toyota Prius, Auris and Lexus are full hybrids, as these cars can be moved forward on battery power alone. The Toyota brand name for this technology is Hybrid Synergy Drive. A computer oversees operation of the entire system, determining if engine or motor, or both should be running. The ICE will be shut off when the electric motor is sufficient to provide the power.
Medium hybrid ( = motor assist hybrid)
Motor assist hybrids use the engine for primary power, with a torque-boosting electric motor connected in parallel to a largely conventional powertrain. EV mode is only possible for a very limited period of time, and this is not a standard mode. Compared to full hybrids, the amount of electrical power needed is smaller, thus the size of the battery system can be reduced. The electric motor, mounted between the engine and transmission, is essentially a very large starter motor, which operates not only when the engine needs to be turned over, but also when the driver “steps on the gas” and requires extra power. The electric motor may also be used to re-start the combustion engine, deriving the same benefits from shutting down the main engine at idle, while the enhanced battery system is used to power accessories. The electric motor is a generator during regenerative breaking.
Examples:
Honda’s hybrids including the Civic and the Insight use this design, leveraging their reputation for design of small, efficient gasoline engines; their system is dubbed Integrated Motor Assist (IMA). Starting with the 2006 Civic Hybrid, the IMA system now can propel the vehicle solely on electric power during medium speed cruising.
A variation on this type of hybrid is the Saturn VUE Green Line hybrid system that uses a smaller electric motor (mounted to the side of the engine), and battery pack than the Honda IMA, but functions similarly.
Another variation on this type is Mazda’s e-4WD system, offered on the Mazda Demio sold in Japan. This front-wheel drive vehicle has an electric motor which can drive the rear wheels when extra traction is needed. The system is entirely disengaged in all other driving conditions, so it does not enhance performance or economy.
Mild hybrid / micro hybrid (= start/stop systems with energy recuperation)
Mild hybrids are essentially conventional vehicles with oversized starter motors, allowing the engine to be turned off whenever the car is coasting, braking, or stopped, yet restart quickly and cleanly.
During restart, the larger motor is used to spin up the engine to operating rpm speeds before injecting any fuel. That concept is not unique to hybrids; Subaru pioneered this feature in the early 1980s, and the Volkswagen Lupo 3L is one example of a conventional vehicle that shuts off its engine when at a stop.
As in other hybrid designs, the motor is used for regenerative braking to recapture energy. But there is no motor-assist, and no EV mode at all. Therefore, many people do not consider these to be hybrids, since there is no electric motor to drive the vehicle, and these vehicles do not achieve the fuel economy of real hybrid models.
Some provision must be made for accessories such as air conditioning which are normally driven by the engine. Those accessories can continue to run on electrical power while the engine is off.
Furthermore, the lubrication systems of internal combustion engines are inherently least effective
immediately after the engine starts; since it is upon startup that the majority of engine wear occurs, the frequent starting and stopping of such systems reduce the lifespan of the engine considerably. Also, start and stop cycles may reduce the engine’s ability to operate at its optimum temperature, thus reducing the engine’s efficiency.

Powertrain of a mild HEV
Examples:
BMW succeeded in combining regenerative braking with the mild hybrid “start-stop” system in their current 1-series model.
Citroën proposes a start-stop system on its C2 and C3 models. The concept-car C5 Airscape has an improved version of that, adding regenerative breaking and traction assistance functionalities, and supercapacitors for energy buffering.
Plug-in hybrid (= grid connected hybrid = vehicle to grid V2G)
All the previous hybrid architectures could be grouped within a classification of charge sustaining: the energy storage system in these vehicles is designed to remain within a fairly confined region of state of charge (SOC). The hybrid propulsion algorithm is designed so that on average, the SOC of energy storage system will more or less return to its initial condition after a drive cycle.
A plug-in hybrid electric vehicle (PHEV) is a full hybrid, able to run in electric-only mode, with larger batteries and the ability to recharge from the electric power grid. Their main benefit is that they can be gasoline-independent for daily commuting, but also have the extended range of a hybrid for long trips.
Grid connected hybrids can be designed as charge depleting: part of the “fuel” consumed during a drive is delivered by the utility, by preference at night. Fuel efficiency is then calculated based on actual fuel consumed by the ICE and its gasoline equivalent of the kWh of energy delivered by the utility during recharge. The “well-to-wheel” efficiency and emissions of PHEVs compared to gasoline hybrids depends on the energy sources used for the grid utility (coal, oil, natural gas, hydroelectric power, solar power, wind power, nuclear power).
In a serial Plug-In hybrid, the ICE only serves for supplying the electrical power via a coupled generator in case of longer driving distances. Plug in hybrids can be made multi-fuel, with the electric power supplemented by diesel, biodiesel, or hydrogen.
The Electric Power Research Institute’s research indicates a lower total cost of ownership for PHEVs
due to reduced service costs and gradually improving batteries.
Some scientists believe that PHEVs will soon become standard in the automobile industry. Plug-in vehicles which use batteries to store electric energy outperform cars which use hydrogen as carrier for the energy taken from the grid. The following figures indicate the efficiencies of a hydrogen fuel cell HEV and a battery powered EV.
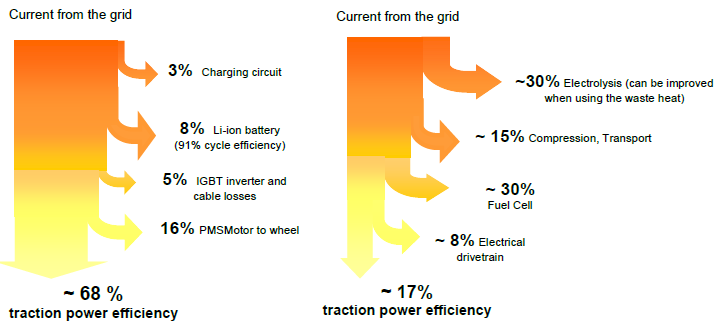
Traction power efficiency of a plugged EV.
Left a battery powered plug in EV (Mitsubishi Lancer Evolution MIEV)) Right a Fuel Cell EV (Mercedes NECAR 3)
For typical driving cycles, the achieved efficiencies are lower. The battery powered EV achieves efficiencies in the range of 50 to 60%. The hydrogen powered EV has a total efficiency of about 13% only at those drive cycles.
Examples:
Mercedes BlueZERO E-CELL PLUS (concept car): series HEV. Opel Ampera: series HEV.

Plug-in-Hybrid Opel Ampera
The Plug-in-Hybrid Volvo C30 (concept car) is a series HEV. It has a 1,6 liter gasoline/bio-ethanol ICE. A synchronous generator charges the Li-polymer battery (ca. 100 km autonomy) when the battery SoC is lower than 30%. There are four electric wheel-motors.

Plug-in-Hybrid Volvo C30
3. Types by nature of the power source
Electric-internal combustion engine hybrid
There are many ways to create an electric-internal combustion hybrid. The variety of electric-ICE designs can be differentiated by how the electric and combustion portions of the powertrain connect (series, parallel or combined), at what times each portion is in operation, and what percent of the power is provided by each hybrid component. Many designs shut off the internal combustion engine when it is not needed in order to save energy, see 2.3.
Fuel cell hybrid
Fuel cell vehicles have a series hybrid configuration. They are often fitted with a battery or supercapacitor to deliver peak acceleration power and to reduce the size and power constraints on the fuel cell (and thus its cost). See 1.1.
Human power and environmental power hybrids
Many land and water vehicles use human power combined with a further power source. Common are parallel hybrids, e.g. a boat being rowed and also having a sail set, or motorized bicycles. Also some series hybrids exist. Such vehicles can be tribrid vehicles, combining at the same time three power sources e.g. from on-board solar cells, from grid-charged batteries, and from pedals.
The following examples don’t use electrical power, but can be considered as hybrids as well:
Pneumatic hybrid
Compressed air can also power a hybrid car with a gasoline compressor to provide the power. Moteur Developpement International in France produces such air cars. A team led by Tsu-Chin Tsao, a UCLA mechanical and aerospace engineering professor, is collaborating with engineers from Ford to get Pneumatic hybrid technology up and running. The system is similar to that of a hybrid-electric vehicle in that braking energy is harnessed and stored to assist the engine as needed during acceleration.
Hydraulic hybrid
A hydraulic hybrid vehicle uses hydraulic and mechanical components instead of electrical ones. A variable displacement pump replaces the motor/generator, and a hydraulic accumulator (which stores energy as highly compressed nitrogen gas) replaces the batteries. The hydraulic accumulator, which is essentially a pressure tank, is potentially cheaper and more durable than batteries. Hydraulic hybrid technology was originally developed by Volvo Flygmotor and was used experimentally in buses from the early 1980s and is still an active area.
Initial concept involved a giant flywheel (see Gyrobus) for storage connected to a hydrostatic transmission, but it was later changed to a simpler system using a hydraulic accumulator connected to a hydraulic pump/motor. It is also being actively developed by Eaton and several other companies, primarily in heavy vehicles like buses, trucks and military vehicles. An example is the Ford F-350 Mighty Tonka concept truck shown in 2002. It features an Eaton system that can accelerate the truck up to highway speeds.